Seven common misconceptions about robotics components
June 18, 2023
Robots are now commonplace in the manufacturing sector as more businesses embrace automation to drive their productivity.
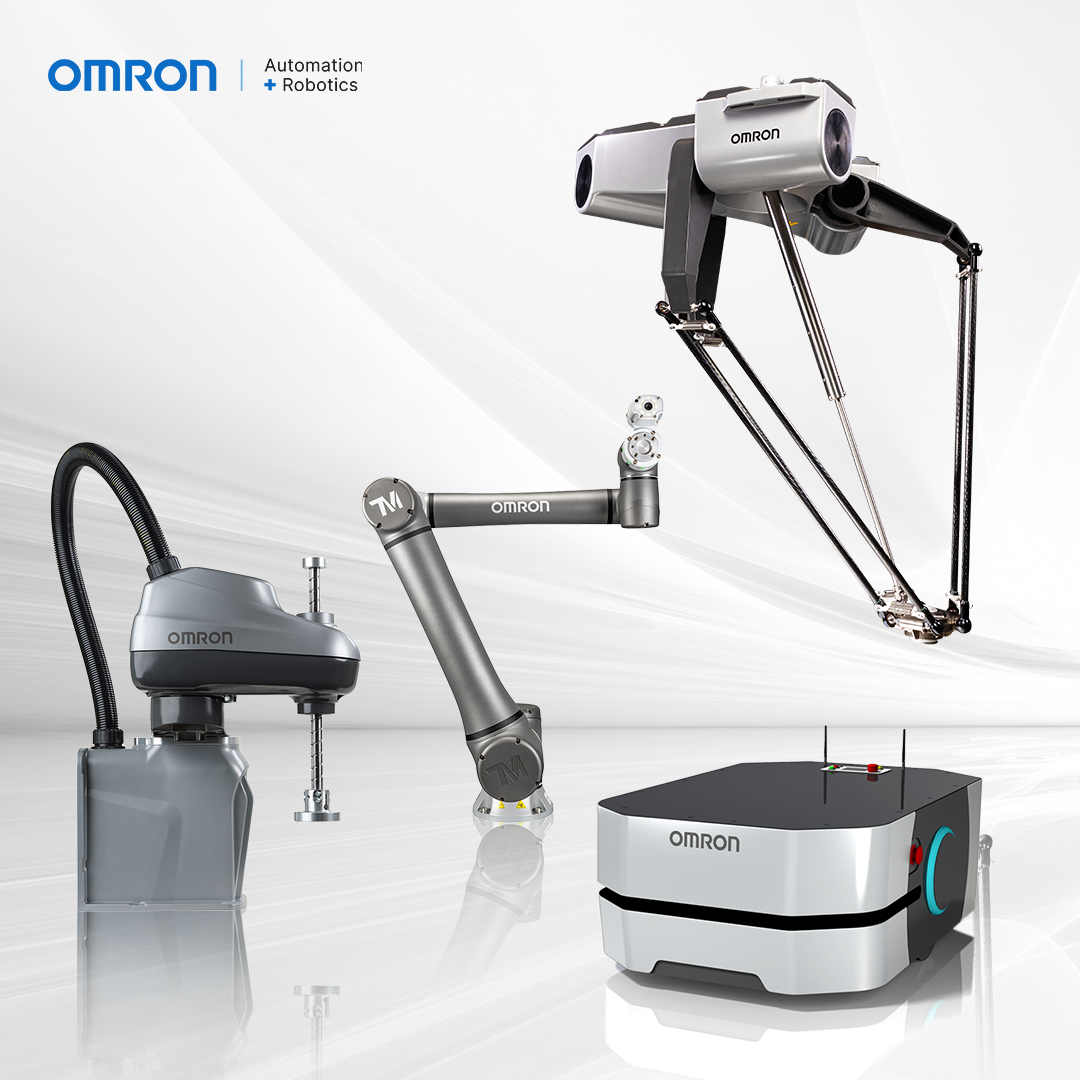
Robots are now commonplace in the manufacturing sector as more businesses embrace automation to drive their productivity.
But despite a huge growth in sales in recent years many SMEs still think robotics may not be a viable option for their manufacturing business.
Maybe, it’s time for a rethink?
Most of the concerns surrounding robotics relate to cost, safety, complexity, programming and maintenance.
But with careful planning and new advances in technology, manufacturers can overcome most of those concerns.
We’ve identified seven common misconceptions about robotics components, namely:
Robotics is unfordable and will add to my factory operating costs
Many SMEs assume that robotics is an expensive investment.
Not true. While the initial cost may be high, manufacturers can save thousands of dollars in reduced costs and improved productivity.
Robots are more affordable than human workers in the long run – and can reduce the costs of goods for consumers.
New technology advancements and a sharp rise in production are making robotics more affordable than ever. Over the past 30 years, the average robot price has dropped by almost 60% in some cases – and prices continue to tumble.
Robotics delivers immediate ROI and users can often pay back their purchase price within months.
I don’t have enough space in my factory for robots and components
Previously, industrial robots were massive, Factories needed extra space to operate them. We’ve all seen images of those giant machines working on automotive production lines. They needed plenty of space and were kept far away from people for safety reasons.
Modern robots use space efficiently. They are flexible and can be adapted for existing facilities.
Collaborative robots (cobots) can work alongside human workers without the need for special guarding.
Robots are prone to accidents and may be unsafe in my workplace
Industrial robots are perceived by many as being dangerous on the factory floor – they are big, hulky pieces of equipment moving at lightening speeds. Older machines did not have advanced sensory capabilities to detect nearby humans, making them prone to dangerous collisions and accidents. For this reason, many manufacturers had to add cages or dividers to separate robots from their human co-workers.
More recently, with the introduction of collaborative robots, which are smaller, lighter and designed specifically for work with humans, workplace safety has improved significantly. Cobots come with an internal safety mechanism designed to minimise workplace accidents and injuries.
And new technologies like light curtains, laser scanners and presence-sensing devices are widely accepted as a method of increasing human safety.
As an added bonus, robotics automation removes workers from dangerous work environments with extreme heat or cold, poor air quality and toxic or hazardous materials. Industrial robots can also take over difficult, dangerous tasks such as manual lifting to reduce the risk of injuries, fatigue and high employee turnover rates.
Robots are difficult to program and operate
Today’s industrial robots and components are much easier to use.
Most modern robots don't need a specialised programmer. Embedded with an easy to operate and understand user interface, anyone can operate these robots, with minimal or no training.
And today’s industrial robots are easy to deploy. Advances in computing power, software-development techniques, and networking technologies have made assembling, installing, and maintaining robots faster and less costly.
Robots are costly to maintain
Of course, manufacturers must consider maintenance costs and the need for extra components when investing in robotics. The good news is that modern robots are more reliable and less likely to breakdown. If they do breakdown, the cost of repairs is now far more affordable.
Robots can’t do most jobs as well as humans
Industrial robots can do many things better than human workers. They’re stronger, faster, and more efficient at easily automated tasks than humans.
Unlike people, robots don’t need to take a break. They don’t get tired and can work 24/7 without interruption if needed.
They can also improve product quality. People make errors, robots don’t. Industrial robots can produce a consistent and regular product to improve both quality and consistency in manufacturing.
Robots aren’t energy efficient
Robots can run 24/7 in factories if required to keep up with demand. They do not require lights to be on, thus reducing energy use.
Also, with computer-powered precision, less material is wasted in the creation of products, to achieve more sustainable manufacturing.
The bottom line is that industrial robots have been proven to simplify human work, bring a fast ROI for manufacturers and streamline production. They are affordable, easy to use and safe.
Omron Automation + Robotics is a world-leading supplier of industrial robots and components.
Our top quality robotics automation products are suitable for a broad range of industrial-related tasks and processes.
Our unique combination of robots, software and integrated control architecture address today's factory automation challenges.
Want to learn how Omron robotics can boost your productivity and performance?
Contact our expert team to find out more.